Best Of
An In-Depth Guide To Build A Better Work Order Process
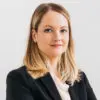
Article written by Kate Williams
Product Marketing Manager at SurveySparrow
14 min read
26 May 2025
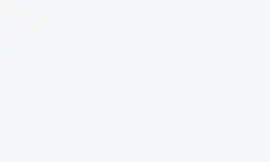
Have you played the “Chinese whisper” game before? The game which is quite popular as the “telephone” game?
No?
Well, it’s a pretty simple game where a message is given to a person, and they pass it on to others just by whispering. The fun lies in the fact that each time someone passes the message, it changes its originality.
This game brings major nostalgia from our childhood. But why are we suddenly talking about this?
Because just like this game, miscommunication can happen in business also. Often, when the message is complex, we fail to deliver it from one person to another. In business, such mistakes can take a turn for the worse. That’s why we need written communications.
Written communications like work order is a permanent record of valuable information.
When working with a team, using work orders to deliver the important messages makes the process easier. Especially if it’s on a digital platform, it helps you access the information quickly.
However, 75% of companies still use traditional methods like paper and spreadsheets to handle their work process.
In this digital era, using traditional methods to generate work order processes can create a lot of hassle and take a lot of time.
That’s why it’s crucial to use a modern work order process to keep your business growing. And, this blog is all about that.
What is a Work Order?
Work orders are the core of your organization’s overall maintenance process. When it’s done right, it ensures each activity related to asset maintenance is completed.
Let’s give it a more detailed definition. A request submitted by a business, a customer, or maybe created in-house within your organization to get a task done is typically known as a work order.
You can apply work orders to any task that needs attention within an organization. It is a digital form or a piece of paper filled out to gather information about a job and start completing the work.
So, Who Uses Work Order?
A lot of industries. From property management companies to manufacturing and from medical equipment service providers to Saas companies, everyone uses work orders.
The goal of building a good process is to streamline the maintenance service and complete every task efficiently. For example, the field service industry uses work orders to efficiently control various maintenance jobs that their customers need.
Computer service management companies use work order requests to manage their customers’ computer-related issues, techs, and expenses.
Not only technicians but work order requests may also come from your customers. Let’s say you’re running a property maintenance company.
Your customers can use a work order request for getting their AC repaired.
Get an idea of how it works here!
What Is The Work Order Process?
A customer calls Steve, the supervisor of a Saas company, for a new product or feature request. Steve creates a work order form, including the customer’s name, location, task info, needs, and other required information.
Then he checks in with the product development team for their availability. And, after a short meeting, he assigns the work order to them.
The development team acknowledges the frustration of the customer and starts working to fulfil the requirement. And after a couple of weeks, the development team gets the job done, documents the timeline, fills a work order completion form and notifies Steve that the work is all done.
This way, the company resolved their customer’s problems, boosted customer satisfaction, and completed the work order successfully!
Now this example must’ve given you a rough idea of what a work order process is. Every work order life cycle has three stages- requested, completed, and documented.
You can break down these stages into more steps.
Having a clear idea about each step ensures maintenance tasks don’t get stuck anywhere. And don’t worry, we’re here to help you with this, taking maintenance as an example. Excited? Let’s begin.
The Task Identification
The first stage of the process is identifying a task or the need for a work order. Maintenance tasks can be divided into two ways- planned and unplanned maintenance.
When you can identify all the maintenance tasks from routine inspection and ahead of time, they are known as planned maintenance.
When you can’t foresee a future maintenance issue or, rather say, usage-based malfunctions, it is known as unplanned maintenance. However, unexpected or planned, once a need for maintenance occurs, the work order process begins.
The Requester Creates The Maintenance Request
Every little detail of the task is collected and submitted to the maintenance team in this second phase of the work order lifecycle.
If a machine breaks down or a fault needs proper maintenance, the team starts building a work order request form.
Work Order Gets Approved & Scheduled
In this stage, a maintenance manager approves the request. If the requested maintenance needs any special equipment to complete the task, it is acquired in this stage.
After that, the maintenance manager or team ensures each task is well-prioritized based on:
- Urgency
- Impact of issue
- Readiness of the team
- Technician’s skills
After prioritizing, you can schedule the work order based on deadline, maintenance triggers, etc. A deadline helps keep the team accountable for their work, ultimately getting the job done in time.
The Work Order Is Completed
After prioritizing the task, it’s given to a technician for further action. The technician takes all the necessary action for completing the maintenance task. Be it complex maintenance or repairing jobs or easy ten-minute inspection of machine parts, they try to complete the work order within a deadline.
The Work Order Is Recorded or Documented
Once the work is done, it’s time for documentation. It’s essential to have a work order log to document all the processes, build asset histories, and prepare audits. A work order log helps identify any missed step. If another issue comes up in the future, it helps to give an alternative solution.
The Work Order Gets Analyzed
So, when the work process is closed and adequately documented, it’s time for reviewing or analyzing the work order from time to time. Regular work order review ensures the machine or equipment is working perfectly.
It’s necessary to follow a process to maintain the team’s accountability and deliver the work on time. The work order process can vary based on the work complexity. However, having an idea about these fundamental processes can help you see how it fits your company’s workflow and allows you to improve on it.
3 Ways To Build A Better Work Order Process
Having a well-defined work process helps to increase productivity. A disorganized process may result in lost time, money, and productivity. And no one wants that, right? So, it’s crucial to know how to build a better work order that establishes more accountability, streamlines workflows and reduces risks.
Invest In A Good Software
Investing in good work order software will give you the authority to manage the work process smoothly. With software, requesters can submit their work orders in a blink of an eye. And the best part is you don’t have to put any effort into assigning and scheduling the work order for maintenance tasks. The software automatically notifies the appropriate person to allocate and approve the work.
With such software, your team can record how much time they’ve spent on a project, what equipment they’ve used, etc. This will help you keep a better track of inventory counts and labor allocation. Wait, there’s more! A work order software also offers a platform for open communication. The technicians can easily notify their maintenance manager about the work order, necessary changes, updates, and completion.
Use Mobile Devices To Complete Work Orders
Long gone are the days where you use a pen and paper to manage the work orders. Using a mobile device to get information and track tasks helps your team manage their work orders from anywhere and anytime. 69% of IT decision-makers believe that BYOD (Bring Your Own Device) policies are valuable for any workplace. It saves your employees valuable time. Sometimes, your maintenance team may need to send a note, ask a question while working in the field. So, giving them a device that allows them to communicate makes them more efficient and productive.
Prioritize Work Order & Gather the Right Information
Incorrect information won’t help you complete the task perfectly. It’s always vital to collect the correct work order information. For example, suppose a requester requests maintenance for a specific machine component, and your maintenance manager or supervisor gets the incorrect information. In that case, your maintenance team will invest their work time in a different machine component. And the right one won’t get fixed. So, keep the information legit.
Also, make sure to prioritize your work order wisely. We all know that it’s impossible to manage everything at once. That’s why prioritizing tasks helps a lot to complete work in a scheduled time.
Different Work Order Management Methods
Simply building a work order process doesn’t give the assurance for success. You have to learn how to manage the work orders efficiently. A perfect work order management system is crucial for smoothly operating the work order lifecycle. Work order management helps to ignore all the issues related to low accountability, high downtime, and higher costs. Several organizations use different management methods. Regardless of the method you choose for your organization, let’s take a look at all of them with their pros and cons.
Pros and Cons of Work Order Systems:
Pen and Paper
Pen and paper are the most traditional method of managing work orders. Since the work order concept was invented, organizations use printed forms to request, complete, and document their maintenance process. In this method, a single piece of printed paper or form travels from the internal or external (customers) requester to the maintenance team.
Pros:
- Relying on pen and paper can help small organizations with few work orders.
- Relying on pen and paper is costs effective.
- Comforting to use. Using pen and paper to build a work order requires no training.
Cons:
- Paper forms or documents are damageable. The maintenance team can quickly lose them.
- Papers take time to sort, find and retrieve.
- Papers are not ideal for time-sensitive work orders.
Spreadsheet
Excel and Google Sheets play a significant role in eliminating the need for using a paper form to take work orders. With Google Sheets, there’s a low risk of losing your files. With spreadsheets, it’s easier to create reports and search for information.
Pros:
- From mobile devices to laptops, you can access spreadsheets from anywhere.
- With spreadsheets, it’s difficult to lose or damage the work order file.
Cons:
- It’s not easy to damage the data in a spreadsheet. However, the work order requests can get deleted if many people access the document simultaneously.
- There’s a risk of the system getting bogged down.
Whiteboard
A Whiteboard work order system is another traditional way for asset maintenance. In this method, the requester fills a paper form to request maintenance. After gathering the information, the maintenance manager organizes it on a whiteboard instead of a paper or other spreadsheet.
Pros:
- A whiteboard helps to visualize the requester’s information efficiently.
- Whiteboard is a cost-effective method.
Cons:
- This method has a high risk of damaging or losing the work orders.
CMMS Software
CMMS Software or Computerized Maintenance Management System is one of the most helpful work order management methods. It helps to automate every work order process. The requesters can easily submit their requests virtually. Once submitted, the software will automatically schedule and assign the work order task to the available technician. As of 2018, nearly 53% of companies use CMMS Software to monitor their maintenance. While 44% of them still use paper!
Pros:
- It helps you to prioritize work orders, assign and schedule them to the right persons and complete the orders on time.
- It helps to increase productivity and reduce the backlog.
Cons:
- This system is more expensive than any other work order management system.
- The requesters and technicians must have the training to understand the technology of CMMS software.
Everything You Need to Know About Work Order Form
Work order forms are the heart of the entire work order process. To build a complete work order, you must create a form that captures all the crucial information. A perfect form will include these details;
Form for the requester
- Requester’s Name
- Requester’s contact information (phone number, location, email address)
- The date of request
- The date of maintenance
- The deadline for the maintenance
- Location of the requiring maintenance work order
- Identification number of the work order
- Maintenance or repairing issues noticed by the requester
Form for the completion of work order
- Description of the required maintenance to resolve the work order issue
- If any necessary equipment needed to complete the task
- Schedule time and date for the task
- Estimated time to complete the task
- The name of the assigned technician
- Description or rating of the work performance
- Description or rating of work that had a performance issue
- Timeline for the maintenance
Instead of using paper or pen, modern industry is focusing more on creating digital forms to manage their work order process flow. The reason?
Who likes to bring a physical pad to every inspection and write the complete form on-site!
Answering a paper might be boring for your maintenance team. They may skip a few critical questions too!
So, the modern solution is a work order management software or an online survey software like SurveySparrow.
Yes, you read that right! With SurveySparrow, you can create an engaging work order request form and a work order completion form within a few minutes.
And why should you choose SurveySparrow? Well, we’ve got not 1, but 3 different reasons for it. Here they are;
Easy To Fill:
Filling up these work order forms are enjoyable. SurveySparrow’s conversational question type, the chat-like interface won’t make the work order filling process tiresome.
Also, the platform offers multiple question types like Rank order, Matrix question, Dropdown, Contact form to keep the process exciting for your requesters and maintenance team.
Upload Images:
The manufacturing industry reports nearly 400,000 non-fatal injuries and 300 work-related severe injuries. If your team also faces a similar problem, they can quickly click a picture and upload it to the form.
Multilingual Forms:
The work order form can support more than 50 languages. So, no matter where your company operates globally, it’s suitable for your team and customers.
So, this work order form will help you collect every little detail, even the smallest ones.
You can even store the data securely in a PDF format and use it whenever you want. From organized record-keeping to engaging question format, this form will definitely help you build a better work process.
Wrapping up
We’ve covered almost everything about the work order process. An organized work order management will give you better maintenance results. Also, paper forms are no longer the talk of the town.
They are time-consuming, tiresome, and overwhelming to maintain. It’s the era of using management software that will make the day easier for everyone.
Lastly, the bottom line is, work orders are the heart, brain, blood, and everything of a fantastic maintenance team.
When you manage it with care, it will give your organization the stability, productivity, and efficiency it needs. And ain’t that fantastic?
So, are we successful at convincing you to create a form for your next work order? Feel free to let us know in the comments!
Start 14 Days free trial
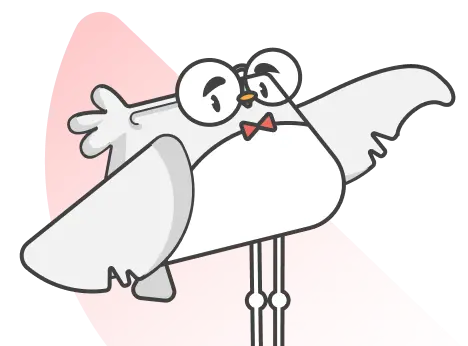

Kate Williams
Excels in empowering visionary companies through storytelling and strategic go-to-market planning. With extensive experience in product marketing and customer experience management, she is an accomplished author, podcast host, and mentor, sharing her expertise across diverse platforms and audiences.
Related Articles
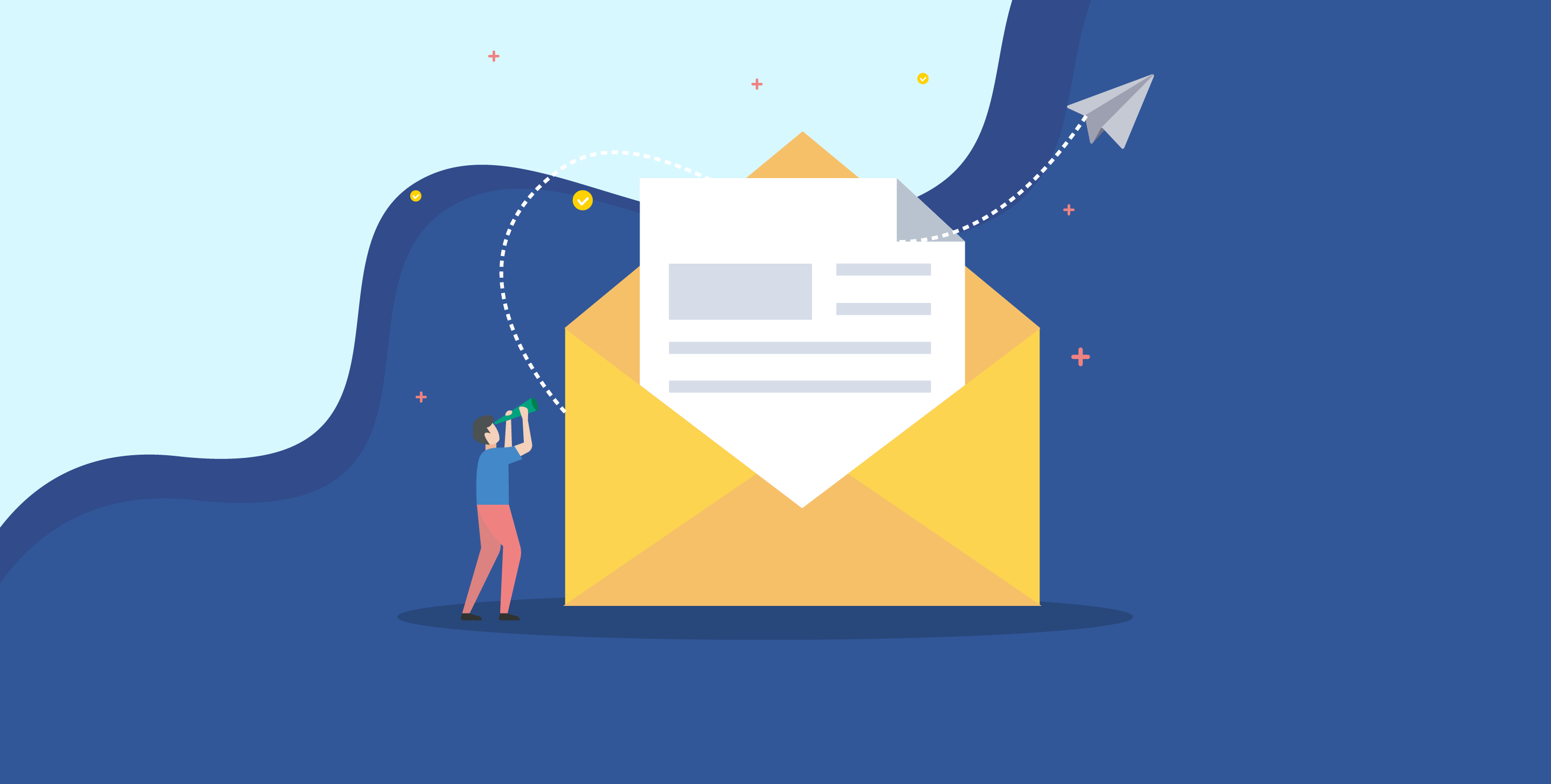
Best Of
13 Best Email Marketing Tools for 2024 for All Businesses
17 MINUTES
6 January 2020
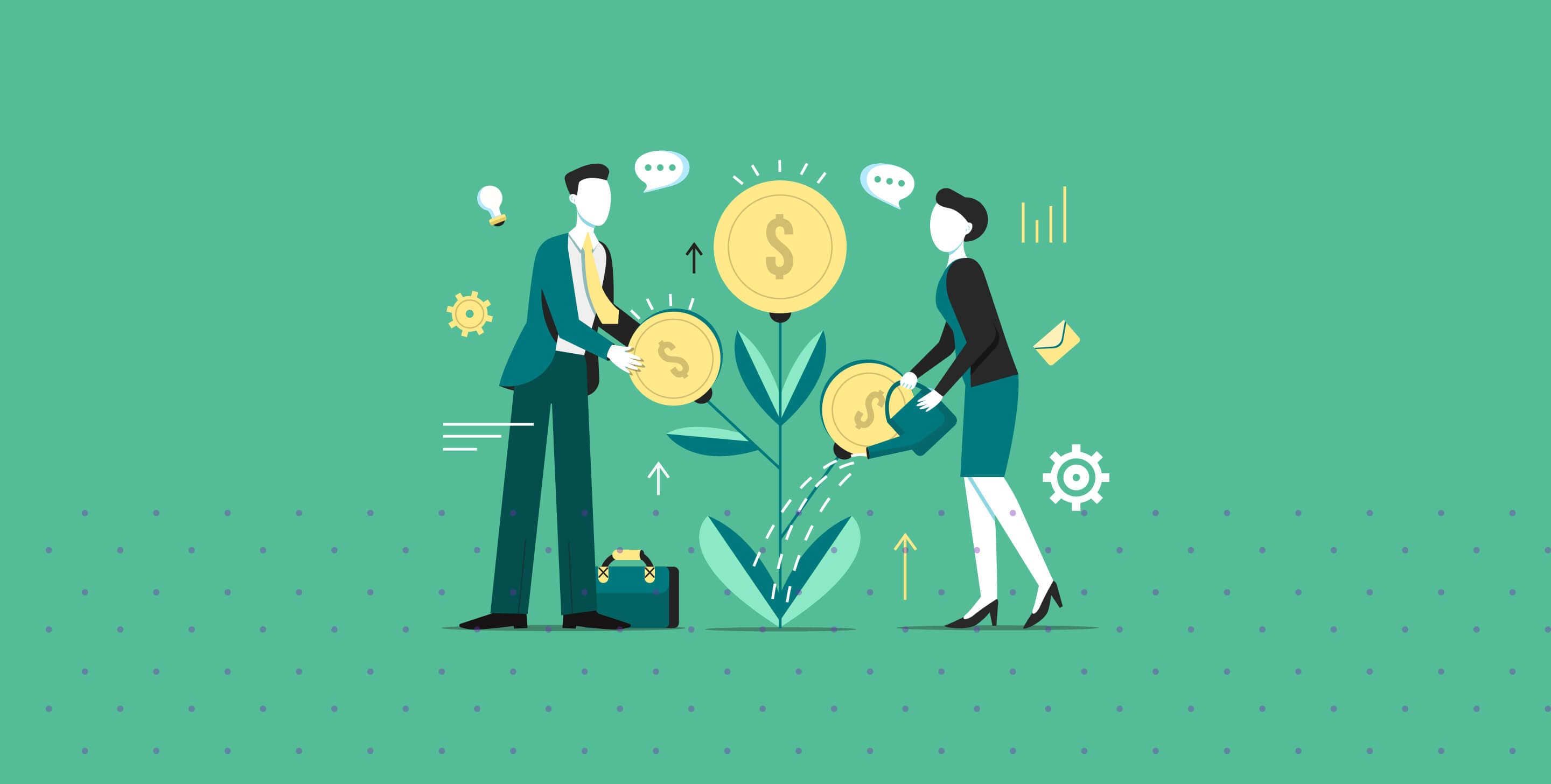
Best Of
Comprehensive Guide on How Surveys Increase ROI
12 MINUTES
21 September 2020
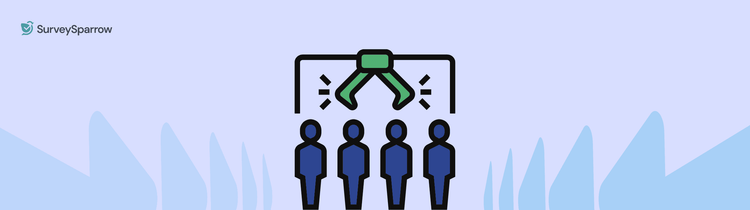
Customer Experience
Simple Random Sampling: A Complete Guide With Examples, Steps & Applications
11 MINUTES
7 October 2022
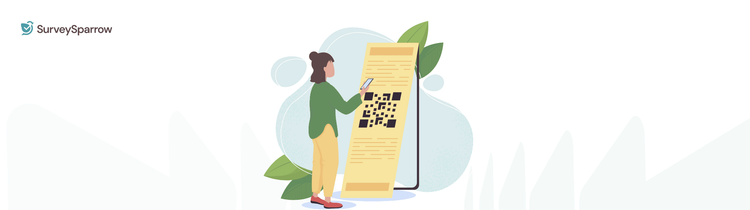
General
QR Code Surveys Made Simple: How-Tos, Benefits & Best Practices
10 MINUTES
12 February 2022