Knowledge
Warehouse Logistics: Elevating Operations Efficiently

Article written by Kate Williams
Content Marketer at SurveySparrow
11 min read
30 June 2025
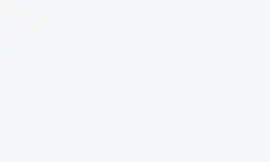
Warehouse logistics is not just about storage. It is a strategic process that optimizes the entire storage process to ensure seamless product movement (Yes, from receiving raw materials to delivering finished products)
So, what exactly is warehouse logistics, and how can it revolutionize your business operations?
Before that, let’s look into some basic terms.
Warehousing
Warehousing is not just finding a place to store stuff. It is about smartly organizing things so they’re easy to find and move around. Think of it as the control center where products are stored strategically for the best efficiency.
Knowing the ins and outs of warehousing is vital for businesses that want to save time and money. A well-organized warehouse minimizes the time spent searching for products. This ultimately cuts operational expenses.
Logistics
Logistics is the smart coordination of all the steps in getting a product from its creation point to your hands.
It handles everything from getting the raw materials needed to make a product to ensuring it reaches customers—no matter the destination’s world postal code—on time. It’s like the strategist who guarantees that every step in the process is smooth and cost-effective.
So, why is logistics so crucial?
In simple terms, efficient logistics helps reduce delays. It cuts unnecessary costs and ensures that products reach customers exactly when they should. From manufacturers to distributors, everything just syncs!
So….
What is Warehouse Logistics?
Warehouse logistics merges warehousing and logistics into a comprehensive strategy.
Warehouse logistics is the process of efficiently managing the storage and movement of goods within a warehouse. It involves strategically organizing products, handling inventory, and coordinating their movement throughout the supply chain.
Simply put, it’s about making sure products move smoothly from the point of arrival to their final destination.
This process is crucial for businesses because it ensures that products are stored efficiently, reducing delays and minimizing operational costs.
Moreover, strategic organization plays a vital role here. What’s that? Amazon, known for its unparalleled efficiency, is a prime example of how strategic warehousing and logistics contribute to business success.
This involves determining the most effective placement of products to facilitate easy access, swift retrieval, and seamless movement within the warehouse. Simultaneously, inventory management becomes critical, ensuring stock levels align with demand.
So, why is this level of management necessary?
Importance of Warehouse Logistics
You must understand everything about the engine that propels successful business operations. Here’s why it is considered so crucial:
1. Swift Order Fulfillment
Speedy Deliveries! Have you ever ordered something and wanted it ASAP?
Efficiently managed warehouses ensure that products are readily available. They reduce the time between order placement and delivery. This agility in meeting customer demands contributes directly to enhanced satisfaction.
2. Cost Reduction
They go hand in hand!
Imagine if a store didn’t know where its products were. Chaos, right? Warehouse logistics stops that confusion. It helps businesses save money by ensuring everything is in its proper place. No more wasting time or losing stuff—just intelligent and cost-effective operations.
3. Operational Efficiency
From efficient storage solutions to seamless product movement, warehouse logistics ensures that every aspect of the supply chain functions cohesively.
4. Competitive Edge
Being quick and accurate is a superpower. (Well, not anymore. It is a necessity)
Companies that nail warehouse logistics must have this superpower. They can process orders fast, deliver on time, and stay ahead of the competition. This reliability becomes a key differentiator in the competitive landscape. It makes them stand out.
5. Customer Satisfaction
However, the end goal is customer satisfaction. The ability to deliver products promptly, without errors, contributes significantly to a positive customer experience. Satisfied customers are more likely to become repeat buyers and brand advocates. When it comes to understanding customer needs, you need an ally. For instance, SurveySparrow seamlessly fits into your logistics plan, ensuring satisfied customers.
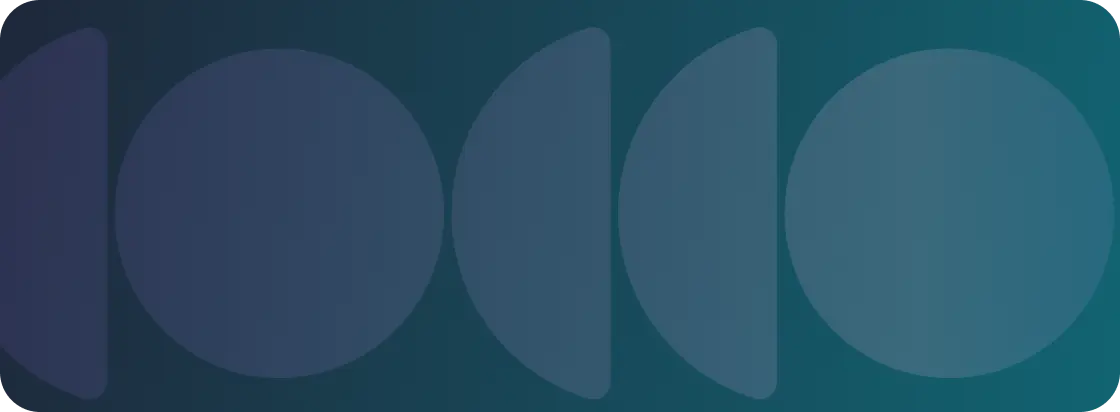
Explore Deeper Customer Insights with SurveySparrow
A personalized walkthrough by our experts. No strings attached!
Trends in Warehouse Logistics
Warehouse logistics evolve with time, especially as new technologies in the warehouse continue to reshape operations. Let’s explore the latest trends, shall we?
1. Automation Revolution
Picture a warehouse where robots and machines work alongside humans. This makes everything faster and more precise. That’s the automation revolution. From smart conveyor belts to robotic pickers, automation transforms warehouses’ operations, enhances efficiency, and reduces human error.
2. Data Analytics Dominance
Data is key. Warehouse logistics is embracing data analytics to make smarter decisions. Imagine knowing exactly how much stock you need and where it should be. That’s the power of data analytics. It provides real-time insights for better inventory management.
3. Sustainability Shift
Being environmentally friendly is no longer just a trend. Warehouse logistics is joining the sustainability movement by adopting eco-friendly practices. Businesses are reducing their carbon footprint while staying efficient by using energy-efficient warehouses for eco-packaging.
4. E-commerce Integration
The growth of online shopping has a vital role to play in this. Warehouses are adapting to handle the e-commerce boom. Warehouse logistics now focuses on seamlessly integrating online orders into the traditional supply chain, with trucking logistics playing a key role in ensuring timely deliveries. Efficient e-commerce logistics mean quicker deliveries and happier online shoppers.
5. Real-Time Visibility
Imagine having a magic crystal ball that shows you exactly where each product is in the supply chain. That’s real-time visibility. It uses systems that offer live updates on inventory, shipments, and order statuses. It’s like ensuring everything is on track.
Benefits of Warehouse Logistics
Let’s break down the benefits that make it a must-have for any successful operation.
1. Faster Operations, Happy Customers:
Fast operations translate to speedy deliveries, and that’s a win for everyone—customers get what they want, and businesses earn their smiles.
2. Cost Savings, More Profits:
Businesses save money using space effectively, cutting down mistakes, and making processes smooth. And when costs go down, profits go up.
3. Smooth-Running Operations:
Think of a well-organized warehouse like a well-oiled machine. From storing products to moving them around, everything works smoothly. It’s like a behind-the-scenes conductor making sure everything plays in harmony.
4. Stay Competitive in the Market:
Being quick matters in business. (Yes, it is a race!)
Warehouse logistics gives businesses a head start. Fast order processing and on-time deliveries set you apart from the competition.
5. Satisfied Customers, Repeat Business:
When customers get what they ordered when they expected it, they’re satisfied. Satisfied customers become repeat customers. It’s a direct connection between efficient warehouse logistics and a returning customer.
6. Accurate Inventory Management:
Warehouse logistics helps businesses know exactly what’s in stock. No more guessing or surprises. Accurate inventory management means always having the right product amount without excess or shortages.
7. Scalability for Business Growth:
As a business grows, warehouse logistics grows with it. It’s a flexible solution that adapts to changes, making it easier for companies to expand without hiccups.
8. Fewer Mistakes, Less Stress:
Efficient warehouse logistics means fewer mistakes. From picking the right products to shipping correct orders, accuracy is crucial. Reducing errors means less stress for both businesses and customers.
9. Efficient Returns Handling:
Returns happen, but with warehouse logistics, handling them becomes more straightforward. Organized systems make the returns process smoother, ensuring a positive customer experience even in challenging situations.
10. Boosted Employee Productivity:
When everything is in order, employees can work more efficiently. Moreover, it isn’t just about products. It’s about creating a workplace where people can do their best work without unnecessary hurdles.
Setting Up a Warehouse: A Practical Guide
Establishing an efficient warehouse involves careful planning and strategic decisions. Let’s explore a step-by-step guide on how to set up a warehouse for optimal functionality.
1. Define Your Warehouse Needs
Begin by understanding the specific needs of your business. Consider the types of products you’ll store, the volume of goods, and any special requirements. This foundational step sets the stage for a practical warehouse layout.
2. Choose the Right Location
Location matters. Select a site that minimizes transportation costs and provides easy access for suppliers and customers. Proximity to major transportation hubs can significantly enhance overall logistics efficiency.
3. Optimize Storage Space
Maximize your storage capacity by choosing the right shelving systems and storage solutions. Consider vertical storage options to utilize the total height of your warehouse. Efficient space utilization is key to minimizing costs.
4. Invest in Material Handling Equipment
Equip your warehouse with the necessary material handling tools. Forklifts, pallet jacks, and conveyor belts can significantly streamline product movement and improve efficiency. Investing in the right equipment pays off in the long run.
5. Implement Efficient Warehouse Layout
Organize your warehouse space logically. Place high-demand products closer to the shipping area for faster retrieval. Create marked aisles and use a systematic approach to arrange products based on their frequency of use.
6. Integrate Technology Solutions
Leverage technology to enhance warehouse operations. Implement a Warehouse Management System (WMS) for real-time inventory tracking, order processing, and data analysis. Embracing technology ensures accuracy and efficiency in your daily operations.
7. Establish Clear Processes
Define and document standard operating procedures (SOPs) for every aspect of warehouse operations. From receiving shipments to order fulfillment, be transparent. It minimizes errors and ensures consistency.
8. Prioritize Safety Measures
Create a safe working environment for your warehouse team. Implement safety protocols, provide proper training, and ensure the use of personal protective equipment. A safe workplace contributes to employee well-being and operational efficiency. It can be challenging to balance multiple priorities in a warehouse environment, where safety, efficiency, and productivity all demand attention. The SQCDP framework offers a structured approach to achieving operational control while managing risks effectively.
9. Monitor and Adapt
Regularly monitor warehouse performance and adapt to changing needs. Analyze data from your WMS to identify areas for improvement. Flexibility and continuous improvement are crucial for long-term success.
10. Embrace Sustainable Practices
Consider incorporating eco-friendly initiatives in your warehouse setup. From energy-efficient lighting to waste reduction programs, adopting sustainable practices benefits the environment and aligns with modern business expectations.
What is Warehouse Logistics Management?
Warehouse logistics management is the strategic coordination of all activities within a warehouse, aiming to make operations smooth and efficient. This involves organizing tasks like receiving shipments, storing products, and processing orders in a way that minimizes delays.
Key aspects include precise inventory control, clever use of space, and the strategic placement of high-demand products for quick access. Technology, like Warehouse Management Systems, tracks inventory in real-time.
Also, logistics management software extends beyond the warehouse, coordinating transportation activities and ensuring change adaptability. The ultimate focus is creating cheerful customer experiences through accurate orders and timely deliveries.
Challenges in Warehouse Logistics Management
Running a warehouse isn’t always smooth sailing. There are challenges to tackle.
- Inventory Management Challenges: Keeping track of what’s in stock and its location can be a puzzle, leading to potential errors and delays.
- Space Utilization Hurdles: Efficiently using warehouse space while ensuring easy product access presents a continuous challenge.
- Order Accuracy and Timeliness: Getting orders right and ensuring on-time shipping can be a delicate balancing act, especially during peak periods.
- Technological Hiccups: While technology, like Warehouse Management Systems, can be a boon, integrating it seamlessly and ensuring everyone is on board can pose challenges.
- Transportation Coordination Issues: Coordinating transportation activities and optimizing delivery routes can be complex, impacting overall logistics efficiency.
- Adaptability to Changes: Staying adaptable to changes in demand, market trends, and technology requires ongoing effort and flexibility.
- Communication Challenges: Effective communication between departments and teams is crucial for streamlined warehouse operations.
- Training and Employee Skills: Ensuring warehouse staff are adequately trained and possess the necessary skills for their roles is an ongoing challenge.
- Security Concerns: Protecting warehouse inventory from theft and damage presents a constant challenge that requires vigilant security measures.
- Cost Management Challenges: Balancing the costs associated with warehouse operations, including labor, technology, and maintenance, requires careful financial management.
Wrap Up!
Making your warehouse work smartly is critical. Again, warehouse logistics isn’t just about storing stuff—it’s the secret to saving money, keeping customers happy, and staying competitive. Embrace technology, ensure adaptability, and focus on customer needs.
Customer experience is the answer. Make it a winning game by signing up with SurveySparrow!
(Psst…it’s free to try)
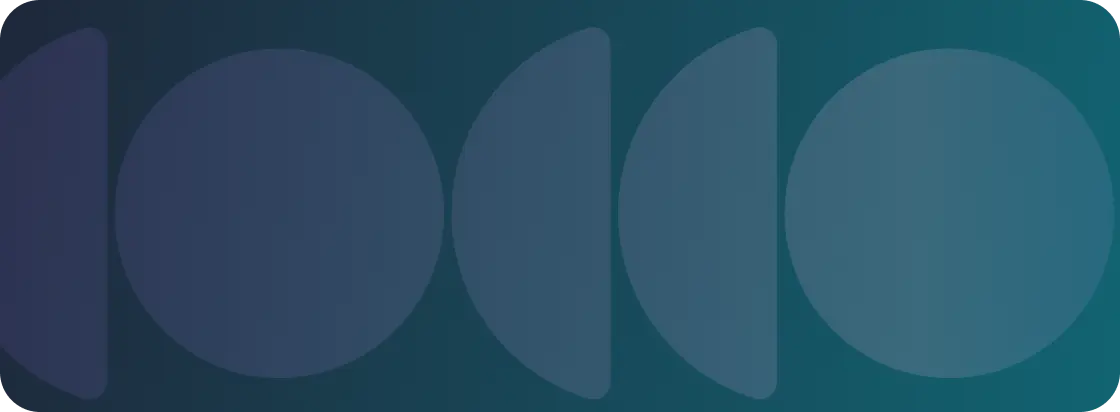
Explore Deeper Customer Insights with SurveySparrow
A personalized walkthrough by our experts. No strings attached!
Start 14 Days free trial
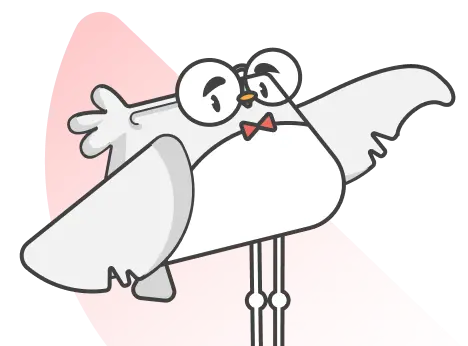
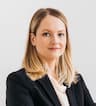
Kate Williams
Related Articles

Knowledge
Exploratory Research: Your Guide to Unraveling Insights
11 MINUTES
20 October 2023
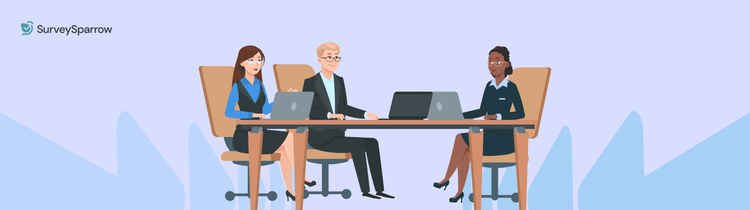
General
What is Situational Analysis? A Beginner's Guide
12 MINUTES
13 November 2024

Knowledge
Big Data Security: Best Practices for Protecting Data
8 MINUTES
6 October 2024

Knowledge
Top 10 HIPAA Compliant Survey Tools: Safeguarding Your Health Data
17 MINUTES
18 December 2023